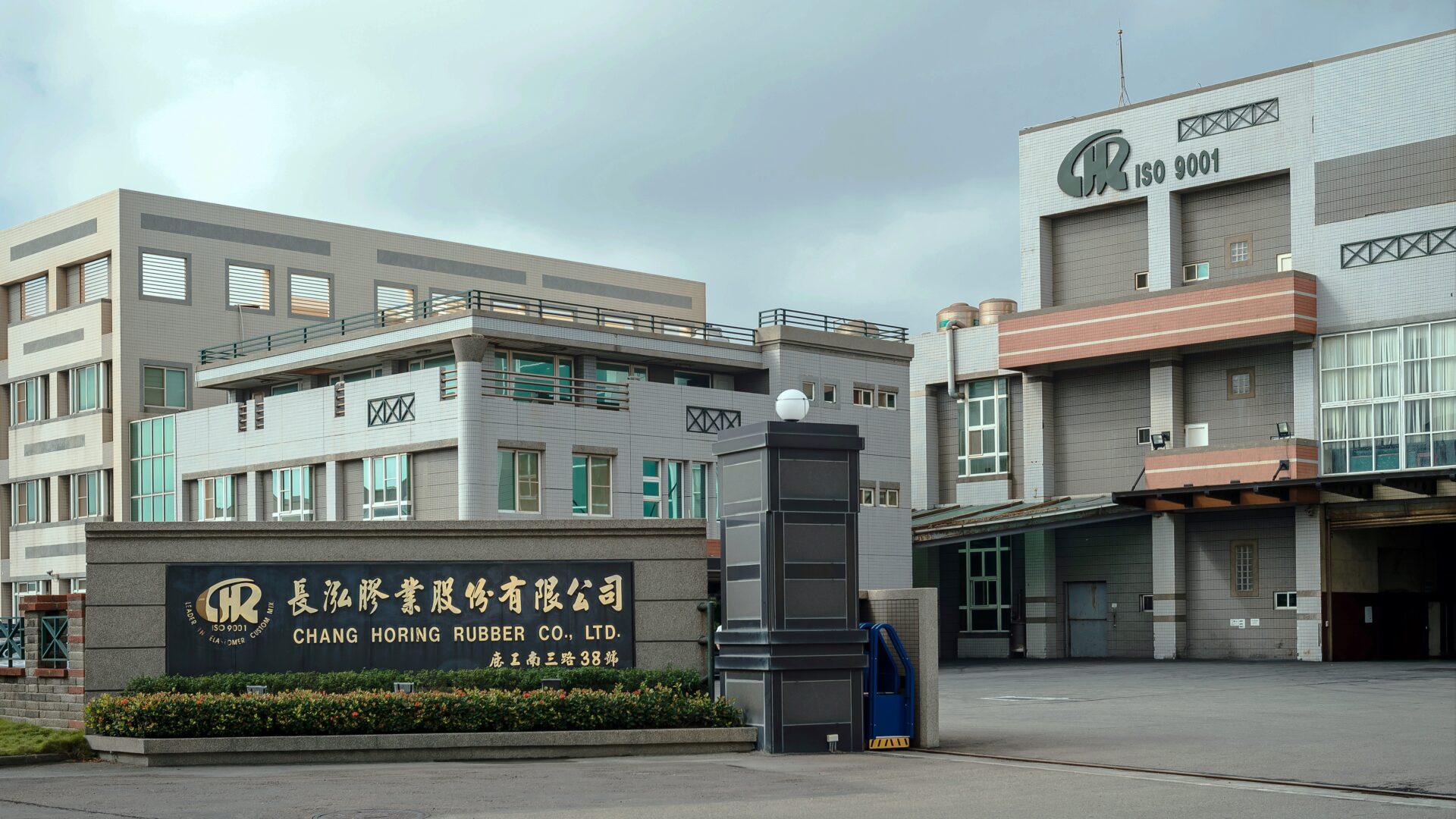
About rubber compounds
Our official Partners in rubber compound supply is CHANG HORING RUBBER Co LTD based in Taiwan.
CHR has been the leader in the compound industry for over 20 years. CHR has been dedicated to develop and customise rubber compound for customers in various industries including automotive, chemical, heavy duty, food and water industry.
For the past 20 years, CHR team has worked closely with customers to meet their specifications and expectations. And all Factories are equipped with systems and instruments that ensure high quality consistency and precision.
Mixing
In General rubber compound is a raw rubber mixed with Other chemical substances that will increase the properties and performance of the rubber and Later on Vulcanising it which creates crosslinks which hardens and improves the elasticity of the rubber.
Good dispersion and distribution of the materials within the compound are Key elements in achieving good quality and uniform final products. The distribution of a compound refers to how uniformly the ingredients are mixed ensuring overall homogeneity.
The dispersion instead describes how uniform the particles are. The ingredients after mixing should not be clumped together, this means that they are not adequately dispersed.
Solid materials like fillers must be broken down to achieve optimum dispersion. It is possible for a compound to be well distributed but poorly dispersed. We calculate all the aspects and provide optimum time and strainers wherever required to achieve compounds with good dispersion and distribution.
Black compound Master-batch
We have developed dedicated supply of Carbon black master batches with separate production lines and different types of carbons based on each requirements.
Carbon Black increases the strength, abrasion resistance and weathering properties as it absorbs harmful UV radiation.
Colour compound Master-batch
We have developed compounds with Multiple colours including Metal, fluorescent
colours with exact colour matching with RAL and Pantone colours.
We use specific systems to measure the colour values of coloured rubber compounds.
Colour matching by our R&D department will be more direct due to the easy comparison between desired colour and fabricated colour. This system will ensure
even greater quality control for customers and allows us to have accurate outcome of
desired colour rubber compound.
Special Property Master-batch (Black and Colour)
Some of Our speciality compounds include compounds which we developed and recieved approvals for below applications.
Mastering the Extraordinary
FAM B Automotive
Fuel Hose and Diesel Filters
Water Applications
UL Certified
Electrical Resistance
Rocket Fuel Systems
Rigid Gas Decompression
Adhesive Fibers
Unveiling a Spectrum of Excellence
Nitrile Rubber (NBR)
Nitrile rubber (NBR), also called nitrile-butadiene rubber, an oil-resistant synthetic rubber produced from copolymer of acrylonitrile and butadiene. Its main applications are in fuel hoses, gaskets, rollers, and other products in which oil resistance is required.
Nitrile rubber is mostly used where high oil resistance is required, as in automotive seals, gaskets, or other items subject to contact with hot oils.
Physical & mechanical properties
- Durometer or Hardness Range: 20 – 95 Shore A
- Tensile Strength Range: 200 – 3,500 PSI
- Elongation (Range %):350% – 650%
- Abrasion Resistance: Good to Excellent
- Adhesion to Metal: Excellent
- Adhesion to Rigid Materials: Good to Excellent
- Compression Set:Good to Excellent
- Flex Cracking Resistance: Fair to Good
- Impact Resistance: Fair to Good
- Resilience / Rebound: Good
- Tear Resistance: Good to Excellent
- Vibration Dampening:Fair to Good
Chemical resistance
- Acids, Dilute: Good
- Acids, Concentrated: Poor to Fair
- Acids, Organic (Dilute): Good
- Acids, Organic (Concentrated): Poor
- Acids, Inorganic:Fair to Good
- Alcohol’s:Fair to Good
- Aldehydes:Poor to Fair
- Alkalies, Dilute: Good
- Alkalies, Concentrated: Poor to Good
- Amines: Poor
- Animal & Vegetable Oils: Good to Excellent
- Brake Fluids, Non-Petroleum Based:Poor
- Diester Oils:Fair to Good
- Esters, Alkyl Phosphate: Poor
- Esters, Aryl Phosphate: Poor to Fair
- Ethers: Poor
- Fuel, Aliphatic Hydrocarbon: Good to Excellent
- Fuel, Aromatic Hydrocarbon:Fair to Good
- Fuel, Extended (Oxygenated): Fair to Good
- Halogenated Solvents: Poor
- Hydrocarbon, Halogenated: Poor to Fair
- Ketones:Poor
- Lacquer Solvents:Fair
- LP Gases & Fuel Oils:Excellent
- Mineral Oils: Excellent
- Oil Resistance:Good to Excellent
- Petroleum Aromatic: Good
- Petroleum Non-Aromatic: Excellent
- Refrigerant Ammonia:Good
- Refrigerant Halofluorocarbons:R-11, R-12, R-13
- Refrigerant Halofluorocarbons w/ Oil: R-11, R-12
- Silicone Oil:Good
- Solvent Resistance: Good to Excellent
Thermal properties
- Low Temperature Range: Up to -40º C
- Minimum for Continuous Use (Static): -40 º C
- Brittle Point: -45 º C
- High Temperature Range: 100º C to 120º C
- Maximum for Continuous Use (Static): 110ºC
Environmental performance
- Colorability: Excellent
- Flame Resistance: Poor
- Gas Permeability:Fair to Excellent
- Odor:Good
- Ozone Resistance:Fair to Good
- Oxidation Resistance: Good
- Radiation Resistance: Fair to Good
- Steam Resistance: Fair to Good
- Sunlight Resistance: Poor to Good
- Taste Retention: Fair to Good
- Weather Resistance: Fair to Good
- Water Resistance: Good to Excellent
Styrene-butadiene rubber (SBR)
Styrene-butadiene rubber (SBR), a general-purpose synthetic rubber, produced from a copolymer of styrene and butadiene. SBR is used in great quantities in automobile and truck tires, generally as an abrasion-resistant replacement for natural rubber. It has excellent abrasion resistance, crack resistance, and better aging characteristics
Applications include belting, flooring, wire and cable insulation, and footwear etc
Physical & mechanical properties
- Durometer or Hardness Range: 30 – 95 Shore A
- Tensile Strength Range: 500 – 3,000 PSI
- Elongation (Range %):450% – 600%
- Abrasion Resistance: Excellent
- Adhesion to Metal: Excellent
- Adhesion to Rigid Materials: Excellent
- Compression Set:Good to Excellent
- Flex Cracking Resistance: Good
- Impact Resistance: Excellent
- Resilience / Rebound: Good
- Tear Resistance: Fair to Excellent
- Vibration Dampening:Fair to Good
Chemical resistance
- Acids, Dilute: Fair to Good
- Acids, Concentrated: Poor to Fair
- Acids, Organic (Dilute): Good
- Acids, Organic (Concentrated): Poor to Good
- Acids, Inorganic:Fair to Good
- Alcohol’s: Good
- Aldehydes:Poor to Fair
- Alkalies, Dilute: Fair to Good
- Alkalies, Concentrated: Fair to Good
- Amines:Poor to Good
- Animal & Vegetable Oils: Poor to Good
- Brake Fluids, Non-Petroleum Based:Poor to Good
- Diester Oils:Poor
- Esters, Alkyl Phosphate: Poor
- Esters, Aryl Phosphate: Poor
- Ethers: Poor
- Fuel, Aliphatic Hydrocarbon: Poor
- Fuel, Aromatic Hydrocarbon:Poor
- Fuel, Extended (Oxygenated): Poor
- Halogenated Solvents: Poor
- Hydrocarbon, Halogenated: Poor
- Ketones:Poor to Good
- Lacquer Solvents:Poor
- LP Gases & Fuel Oils:Poor
- Mineral Oils: Poor
- Oil Resistance: Poor
- Petroleum Aromatic: Poor
- Petroleum Non-Aromatic: Poor
- Refrigerant Ammonia:Good
- Refrigerant Halofluorocarbons:R-12, R-13
- Refrigerant Halofluorocarbons w/ Oil: Poor
- Silicone Oil:Poor
- Solvent Resistance: Poor
Thermal properties
• Low Temperature Range: Up to -50°C
• Minimum for Continuous Use (Static): – 45 °C
• Brittle Point: -55 °C
• High Temperature Range: 100 °C to 110 °C
• Maximum for Continuous Use (Static): 100°C
Environmental performance
- Colorability: Good
- Flame Resistance: Poor
- Gas Permeability:Fair
- Odor:Good
- Ozone Resistance:Poor
- Oxidation Resistance: Fair to Excellent
- Radiation Resistance: Poor to Good
- Steam Resistance: Fair to Good
- Sunlight Resistance: Poor
- Taste Retention: Fair to Good
- Weather Resistance: Fair to Good
- Water Resistance: Good to Excellent
Ethylene Propylene Rubber (EPDM)
Ethylene-propylene copolymer, also called ethylene-propylene rubber, a class of synthetic rubber produced by copolymerizing ethylene and propylene, usually in combination with other chemical compounds. EPDM has excellent resistance to electricity and ozone and an ability to be processed with a number of additives. They are made into products for use in automotive engines, electrical wiring, and construction
Widely employed in flexible seals for automobiles, wire and cable insulation, weather stripping, tire sidewalls, hoses, and roofing film.
Physical & mechanical properties
- Durometer or Hardness Range: 30 – 90 Shore A
- Tensile Strength Range: 500 – 2,500 PSI
- Elongation (Range %):100% – 700%
- Abrasion Resistance: Good
- Adhesion to Metal: Good to Excellent
- Adhesion to Rigid Materials: Good to Excellent
- Compression Set:Poor to Excellent
- Flex Cracking Resistance: Good
- Impact Resistance: Very Good
- Resilience / Rebound: Fair to Good
- Tear Resistance: Fair to Good
- Vibration Dampening:Fair to Good
Chemical resistance
- Acids, Dilute: Excellent
- Acids, Concentrated: Excellent
- Acids, Organic (Dilute): Excellen
- Acids, Organic (Concentrated): Fair to Good
- Acids, Inorganic:Excellent
- Alcohol’s:Good to Excellent
- Aldehydes:Good to Excellent
- Alkalies, Dilute: Excellent
- Alkalies, Concentrated: Excellent
- Amines:Fair to Good
- Animal & Vegetable Oils Good
- Brake Fluids, Non-Petroleum Based:Good to Excellent
- Diester Oils:Poor
- Esters, Alkyl Phosphate: Excellent
- Esters, Aryl Phosphate: Excellent
- Ethers: Fair
- Fuel, Aliphatic Hydrocarbon: Poor
- Fuel, Aromatic Hydrocarbon:Poor
- Fuel, Extended (Oxygenated): Poor
- Halogenated Solvents: Poor
- Hydrocarbon, Halogenated: Poor
- Ketones:Good to Excellent
- Lacquer Solvents:Poor
- LP Gases & Fuel Oils:Poor
- Mineral Oils: Poor
- Oil Resistance: Poor
- Petroleum Aromatic: Poor
- Petroleum Non-Aromatic: Poor
- Refrigerant Ammonia:Good
- Refrigerant Halofluorocarbons:R-12, R-13
- Refrigerant Halofluorocarbons w/ Oil: Poor
- Silicone Oil:Excellent
- Solvent Resistance: Poor
Thermal properties
• Low Temperature Range: Up to -50°C
• Minimum for Continuous Use (Static): -40°C
• Brittle Point: -55°C
• High Temperature Range: 100 °C to 120 °C
• Maximum for Continuous Use (Static): 100 °C
Environmental performance
- Colorability:Good to Excellent
- Flame Resistance: Poor
- Gas Permeability:Fair to Good
- Odor:Good
- Ozone Resistance:Good to Excellent
- Oxidation Resistance: Excellent
- Radiation Resistance: Good to Excellent
- Steam Resistance: Excellent
- Sunlight Resistance: Excellent
- Taste Retention: Good to Excellent
- Weather Resistance: Excellent
- Water Resistance: Excellent
Chloroprene Rubber (CR)
Neoprene (CR), also called polychloroprene or chloroprene rubber, synthetic rubber produced by the polymerization (or linking together of single molecules into giant, multiple-unit molecules) of chloroprene. A good general-purpose rubber, neoprene is valued for its high tensile strength, resilience, oil and flame resistance, and resistance to degradation by oxygen and ozone;
Principal applications are in products such as wire and cable insulation, hoses, belts, springs, flexible mounts, gaskets, and adhesives, where resistance to oil, heat, flame, and abrasion are required.
Physical & mechanical properties
- Durometer or Hardness Range: 20 – 95 Shore A
- Tensile Strength Range: 500 – 3,000 PSI
- Elongation (Range %):100% – 800%
- Abrasion Resistance:Very Good to Excellent
- Adhesion to Metal: Excellent
- Adhesion to Rigid Materials: Good to Excellent
- Compression Set:Poor to Good
- Flex Cracking Resistance: Good
- Impact Resistance: Good to Excellent
- Resilience / Rebound: Fair to Good
- Tear Resistance: Good to Excellent
- Vibration Dampening:Good to Excellent
Chemical resistance
- Acids, Dilute: Excellent
- Acids, Concentrated: Poor
- Acids, Organic (Dilute): Good to Excellent
- Acids, Organic (Concentrated): Poor to Good
- Acids, Inorganic:Good to Excellent
- Alcohol’s: Excellent
- Aldehydes:Poor to Fair
- Alkalies, Dilute: Good
- Alkalies, Concentrated: Poor
- Amines:Poor to Good
- Animal & Vegetable Oils: Good
- Brake Fluids, Non-Petroleum Based:Fair
- Diester Oils:Poor
- Esters, Alkyl Phosphate: Poor
- Esters, Aryl Phosphate: Poor to Fair
- Ethers: Poor
- Fuel, Aliphatic Hydrocarbon: Poor to Good
- Fuel, Aromatic Hydrocarbon:Poor to Fair
- Fuel, Extended (Oxygenated): Fair
- Halogenated Solvents: Poor
- Hydrocarbon, Halogenated: Poor
- Ketones:Poor to Fair
- Lacquer Solvents:Poor
- LP Gases & Fuel Oils:Good
- Mineral Oils: Fair to Good
- Oil Resistance: Fair
- Petroleum Aromatic: Good
- Petroleum Non-Aromatic: Good
- Refrigerant Ammonia:Excellent
- Refrigerant Halofluorocarbons:R-11, R-12, R-13, R-21, R-22
- Refrigerant Halofluorocarbons w/ Oil: R-11, R-12, R-22
- Silicone Oil:Fair to Excellent
- Solvent Resistance: Fair
Thermal properties
• Low Temperature Range: Up to -45°C
• Minimum for Continuous Use (Static): -35 °C
• Brittle Point: -60°C
• High Temperature Range: 100°C to 110 °C
• Maximum for Continuous Use (Static): 110 °C
Environmental performance
- Colorability: Fair
- Flame Resistance: Fair to Good
- Gas Permeability:Fair to Good
- Odor:Fair to Good
- Ozone Resistance:Good to Excellent
- Oxidation Resistance: Good to Excellent
- Radiation Resistance: Fair to Good
- Steam Resistance: Fair to Good
- Sunlight Resistance: Good to Excellent
- Taste Retention: Fair to Good
- Weather Resistance: Fair to Good
- Water Resistance: Fair to Good
Epichlorohydrin Rubber (ECO)
Epichlorohydrin rubber (ECO) is the modern alternative for PVC/NBR with greater heat resistance of up to 130°C at constant operating temperature with the added advantages of improved ozone and acid resistance.
ECO has properties similar to nitrile rubber but with better heat, oil and petrol resistance. It has low gas permeability and better low temperature flexibility than NBR. It has excellent resistance to acids, alkalis and ozone.
However, it suffers from poor compression set and has a corrosive effect on metals which can increase tooling costs and limit metal bonding applications.
Physical & mechanical properties
- Durometer or Hardness Range: 40 – 90 Shore A
- Tensile Strength Range: 500 – 2,500 PSI
- Elongation (Range %):200% – 800%
- Abrasion Resistance: Fair to Good
- Adhesion to Metal: Fair to Good
- Adhesion to Rigid Materials: Fair to Excellent
- Compression Set:Good to Excellent
- Flex Cracking Resistance: Good
- Impact Resistance: Fair to Excellent
- Resilience / Rebound: Good
- Tear Resistance: Fair to Excellent
- Vibration Dampening:Good
Chemical resistance
- Acids, Dilute: Good
- Acids, Concentrated: Poor to Fair
- Acids, Organic (Dilute): Fair
- Acids, Organic (Concentrated): Poor
- Acids, Inorganic:Fair to Good
- Alcohol’s:Fair to Good
- Aldehydes:Poor
- Alkalies, Dilute: Poor
- Alkalies, Concentrated: Fair to Good
- Amines:Poor to Good
- Animal & Vegetable Oils: Excellent
- Brake Fluids, Non-Petroleum Based:Poor
- Diester Oils:Poor to Good
- Esters, Alkyl Phosphate: Poor
- Esters, Aryl Phosphate: Poor
- Ethers: Good
- Fuel, Aliphatic Hydrocarbon: Good to Excellent
- Fuel, Aromatic Hydrocarbon:Good to Excellent
- Fuel, Extended (Oxygenated): Fair to Good
- Halogenated Solvents: Poor
- Hydrocarbon, Halogenated: Excellent
- Ketones:Fair
- Lacquer Solvents:Fair
- LP Gases & Fuel Oils:Excellent
- Mineral Oils: Excellent
- Oil Resistance: Excellent
- Petroleum Aromatic: Good to Excellent
- Petroleum Non-Aromatic: Poor
- Refrigerant Ammonia:Poor
- Refrigerant Halofluorocarbons:R-12
- Refrigerant Halofluorocarbons w/ Oil: Good to Excellent
- Silicone Oil:Good to Excellent
- Solvent Resistance: Good to Excellent
Thermal properties
• Low Temperature Range: Up tp -35 °C
• Minimum for Continuous Use (Static): -25°C
• Brittle Point: -45 °C
• High Temperature Range: 100 °C to 125 °C
• Maximum for Continuous Use (Static): 120 °C
Environmental performance
- Colorability: Good
- Flame Resistance: Poor to Good
- Gas Permeability:Excellent
- Odor:Good
- Ozone Resistance:Good to Excellent
- Oxidation Resistance: Good to Excellent
- Radiation Resistance: Poor
- Steam Resistance: Fair to Good
- Sunlight Resistance: Good
- Taste Retention: Good
- Weather Resistance: Good
- Water Resistance: Good
Fluorcarbon Rubber (FKM)
FKM (also known as FPM in Europe) rubber compounds are frequently used to resist extreme temperatures and harsh chemicals. The strong carbon-fluorine bonds that make up the polymer structure provide high thermo-chemical resistance, giving excellent ageing characteristics, such aslow compression set at elevated temperatures.
FKM offers excellent resistance to mineral oils and greases, aliphatic, aromatic and some chlorinated hydrocarbons, fuels, silicone oils and greases. Fluorocarbon rubber compounds are available as a copolymer, terpolymer & tetrapolymes
FKM materials for use in low temperature applications, where with a glass transition of -40°C, it is possible to use FKM down to -51°C in service.
Specific grades are also available for use in biofuels,
Types of FKM
FKM Type | Classification Name | Cure system | Fluorine content | Description |
---|---|---|---|---|
Type 1 | FKM A | Bisphenol | 66% | General Purpose with Excellent Mechanical Properties |
Type 2 | FKM B, F, GF | Bisphenol & Peroxide | 60-70% | Improved Oil/ fluid, solvent resistance, Fuel resistance. Peroxide cure provides improved coolant and water resistance |
Type 3 | GLT | Peroxide | 64-67% | Improved low temperature but less chemical resistance |
Type 4 | Aflas | Peroxide | 55% | Excellent resistance to lubricating oils, corrosion inhibitors and coolants |
Physical & mechanical properties
- Durometer or Hardness Range: 50 – 95 Shore A
- Tensile Strength Range: 500 – 2,000 PSI
- Elongation (Range %):400% – 500%
- Abrasion Resistance: Fair to Good
- Adhesion to Metal: Good to Excellent
- Adhesion to Rigid Materials: Fair to Good
- Compression Set:Good to Excellent
- Flex Cracking Resistance: Fair to Good
- Impact Resistance: Good
- Resilience / Rebound: Poor to Fair
- Tear Resistance: Fair to Good
- Vibration Dampening:Fair to Good
Environmental performance
- Colorability:Good to Excellent
- Flame Resistance: Good to Excellent
- Gas Permeability:Good to Excellent
- Odor:Good
- Ozone Resistance:Excellent
- Oxidation Resistance: Excellent
- Radiation Resistance: Fair to Good
- Steam Resistance: Good to Excellent
- Sunlight Resistance: Good to Excellent
- Taste Retention: Fair to Good
- Weather Resistance: Excellent
- Water Resistance: Excellent
Chemical resistance depends on the type of FKM grade.
Acrylic Rubber (ACM)
Polyacrylic elastomers, also called ACM rubbers, are synthetic elastomers composed of acrylic monomers. ACM has outstanding resistance to heat, oxidation and hydraulic oils, good resistance to ozone, and weathering which is superior to nitrile rubber.
However, water and moisture resistance is poor, as is resistance to acids and alkalis. Also low temperature applications are usually limited to approximately -10°C due to low cold temperature flexibility and compression set.
ACM elastomers are primarily used where combined resistance to heat and oils is required. They are often a good alternative to more expensive heat resistant elastomers where service is less than 150 °C.
Typical applications include automotive transmission components like seals and hoses that have to be resistant to hot oil, fuel and many other common automotive lubricants and hydraulic fluids. ACM elastomer have also found use in vibration damping due to its excellent resilience. Other applications include textiles, adhesives, and coatings.
Physical & mechanical properties
- Durometer or Hardness Range: 40-90 Shore A
- Tensile Strength Range: 500 – 2,500 PSI
- Elongation (Range%): 100% – 450%
- Abrasion Resistance: Fair to Good
- Adhesion to Metal: Fair to Good
- Flex Cracking Resistance: Fair to Good
- Impact Resistance: Poor
- Resilience/Rebound: Fair to Good
- Tear Resistance: Poor to Good
- Vibration Dampening: Good to Excellent
Thermal properties
• Low Temperature Range: Up tp -30 °C
• Minimum for Continuous Use (Static): -25°C
• Brittle Point: -45 °C
• High Temperature Range: 150 °C to 175 °C
• Maximum for Continuous Use (Static): 150 °C
Chemical resistance
- Acids, Dilute: Fair
- Acids, Concentrated: Poor to Fair
- Acids, Organic (Concentrated): Poor
- Alcohols: Poor Adhesion to Rigid Materials: Fair to Good
- Aldehydes: Poor Compression Set: Poor to Good
- Alkalies, Dilute: Fair
- Alkalies, Concentrated: Fair
- Amines: Poor
- Animal & Vegetable Oils: Good
- Brake Fluids, Non-Petroleum Based: Poor
- Diester Oils: Good
- Esters, Alkyl Phosphate: Poor
- Esters, Aryl Phosphate: Poor
- Esthers: Poor
- Fuel, Aliphatic Hydrocarbon: Excellent
- Fuel, Aromatic Hydrocarbon: Poor to Good
- Ketones (MEK, acetone): Poor to Good
- Lacquer Solvents: Poor to Good
- LP Gases & Fuel Oils: Good
- Mineral Oils: Good to Excellent
- Oil Resistance: Excellent
- Petroleum Aromatic: Fair
- Petroleum Non-Aromatic: Good
- Refrigerant Ammonia: Fair
- Refrigerant Halofluorocarbons: R-11, R-12, R-13
- Refrigerant Halofluorocarbons w/ Oil: R-11, R-12 , R-13, R22
- Silicone Oil: Excellent
- Water Resistance: Excellent
- Solvent Resistance: Good
Environmental performance
- Colorability: Good
- Flame Resistance: Poor
- Odor: Fair to Good
- Gas Permeability: Good to Excellent
- Ozone Resistance: Good to Excellent
- Oxidation Resistance: Good to Excellent
- Radiation Resistance: Poor to Good
- Steam Resistance Poor
- Sunlight Resistance: Good to Excellent
- Weather Resistance: Excellent
Ethylene-Acrylic Rubber (AEM VAMAC)
Ethylene-acrylic monomer is a terpolymer of ethylene, methyl acrylate, and an acid-containing monomer as a cure site. AEM can replace silicone in certain applications especially high volume requirements where economies of scale are required.
AEM offers high heat resistance, excellent ozone and weather resistance, low temperature flexibility and high tensile strength.
Typical applications are air management, vacuum and engine breather and oil hoses.
AEM, as excellent vibration dampening, excellent heat aging characteristics and good dynamic property retention over a wide, temperature range, resistant to oils, transmission fluids, water, glycol mixtures, and alkalis.
Physical & mechanical properties
- Durometer or Hardness Range: 35 – 95 Shore A
- Tensile Strength Range: 500 – 3,000 PSI
- Elongation (Range %):200% – 850%
- Abrasion Resistance: Good to Excellent
- Adhesion to Metal: Good
- Adhesion to Rigid Materials: Good
- Compression Set:Poor to Good
- Flex Cracking Resistance: Good
- Impact Resistance: Good to Very Good
- Resilience / Rebound: Poor to Fair
- Tear Resistance: Good to Excellent
- Vibration Dampening:Good
Chemical resistance
- Acids, Dilute: Good
- Acids, Concentrated: Poor to Fair
- Acids, Organic (Dilute): Good to Excellent
- Acids, Organic (Concentrated): Poor to Excellent
- Acids, Inorganic:Fair to Good
- Alcohol’s:Good to Excellent
- Aldehydes:Fair to Good
- Alkalies, Dilute: Good to Excellent
- Alkalies, Concentrated: Poor
- Amines: Good
- Animal & Vegetable Oils: Good
- Brake Fluids, Non-Petroleum Based:Poor
- Diester Oils:Poor
- Esters, Alkyl Phosphate: Poor
- Esters, Aryl Phosphate: Poor
- Ethers: Poor
- Fuel, Aliphatic Hydrocarbon: Good
- Fuel, Aromatic Hydrocarbon:Poor to Fair
- Fuel, Extended (Oxygenated): Fair
- Halogenated Solvents: Poor to Good
- Hydrocarbon, Halogenated: Poor
- Ketones:Poor
- Lacquer Solvents:Poor
- LP Gases & Fuel Oils:Poor
- Mineral Oils: Poor
- Oil Resistance: Poor
- Petroleum Aromatic: Poor
- Petroleum Non-Aromatic: Poor
- Refrigerant Ammonia:Poor to Good
- Refrigerant Halofluorocarbons:Poor to Good
- Refrigerant Halofluorocarbons w/ Oil: Poor
- Silicone Oil:Good to Excellent
- Solvent Resistance: Poor
Thermal properties
• Low Temperature Range: Up to -40 °C
• Minimum for Continuous Use (Static): -30 °C
• Brittle Point: -45 °C
• High Temperature Range: 150 °C to 175 °C
• Maximum for Continuous Use (Static): 150 °C
Environmental performance
- Colorability: Good
- Flame Resistance: Poor
- Gas Permeability:Excellent
- Odor:Good
- Ozone Resistance:Excellent
- Oxidation Resistance: Excellent
- Radiation Resistance: Good
- Steam Resistance: Poor to Fair
- Sunlight Resistance: Excellent
- Taste Retention: Fair to Good
- Weather Resistance: Excellent
- Water Resistance: Good to Excellent
Hydrogenated Nitrile Rubber (HNBR)
HNBR is made via selective hydrogenation of the NBR butadiene groups which improves the temperature and ozone resistance considerably. HNBR is widely known for its physical strength and retention of properties after long-term exposure to heat, oil, and chemicals. HNBR has better heat resistance; oxidation resistance; tensile strength and abrasion resistance than standard nitrile (NBR). Also an excellent choice for automotive refrigerant service.
HNBR is resistant to hot water and steam and has good high- and low-temperature performance with regard to its physical properties. In addition, these mixes also have high media and abrasion resistance and good mechanical properties.
Physical & mechanical properties
- Durometer or Hardness Range: 30 – 95 Shore A
- Tensile Strength Range: 1,500 – 3,500 PSI
- Elongation (Range %):90% – 550%
- Abrasion Resistance: Good to Excellent
- Adhesion to Metal: Excellent
- Adhesion to Rigid Materials: Good to Excellent
- Compression Set:Good to Excellent
- Flex Cracking Resistance: Fair to Good
- Impact Resistance: Excellent
- Resilience / Rebound: Good
- Tear Resistance: Good to Excellent
- Vibration Dampening:Fair to Good
Chemical resistance
- Acids, Dilute: Good
- Acids, Concentrated: Fair to Good
- Acids, Organic (Dilute): Good
- Acids, Organic (Concentrated): Fair to Good
- Acids, Inorganic:Fair to Good
- Alcohol’s:Good to Excellent
- Aldehydes:Fair to Good
- Alkalies, Dilute: Good
- Alkalies, Concentrated: Poor to Good
- Amines: Good
- Animal & Vegetable Oils: Good to Excellent
- Brake Fluids, Non-Petroleum Based:Fair
- Diester Oils:Good
- Esters, Alkyl Phosphate: Poor
- Esters, Aryl Phosphate: Poor to Fair
- Ethers:Poor to Fair
- Fuel, Aliphatic Hydrocarbon: Excellent
- Fuel, Aromatic Hydrocarbon:Fair to Good
- Fuel, Extended (Oxygenated): Good to Excellent
- Halogenated Solvents: Poor to Fair
- Hydrocarbon, Halogenated: Poor
- Ketones:Poor
- Lacquer Solvents:Fair
- LP Gases & Fuel Oils:Excellent
- Mineral Oils:Good to Excellent
- Oil Resistance:Good to Excellent
- Petroleum Aromatic: Good to Excellent
- Petroleum Non-Aromatic: Good to Excellent
- Refrigerant Ammonia:Good
- Refrigerant Halofluorocarbons:R-11, R-12, R-13
- Refrigerant Halofluorocarbons w/ Oil: R-11, R-12
- Silicone Oil:Good to Excellent
- Solvent Resistance: Poor
Thermal properties
• Low Temperature Range: Up to -40 °C
• Minimum for Continuous Use (Static): -30 °C
• Brittle Point: -50 °C
• High Temperature Range: 130 °C to 150 °C
• Maximum for Continuous Use (Static): 135 °C
Environmental performance
- Colorability: Excellent
- Flame Resistance: Poor
- Gas Permeability:Fair to Excellent
- Odor:Good
- Ozone Resistance:Good to Excellent
- Oxidation Resistance: Excellent
- Radiation Resistance: Fair to Good
- Steam Resistance: Fair to Good
- Sunlight Resistance: Good to Excellent
- Taste Retention: Fair to Good
- Weather Resistance: Good to Excellent
- Water Resistance: Excellent
Carboxylated Nitrile (XNBR)
XNBR is a nitrile rubber (NBR) with the addition of a carboxyl group to saturate the butadiene segment of the carbon polymer backbone. The added carboxyl group greatly improves the resistance of NBR to abrasive and tear wear without affecting its oil and solvent resistance or its thermal stability.
XNBR based parts are usually applied in dynamic assembly such as seals and rod wipers, V- belts, High abrasion resistance shoes, O-rings, Printing rolls, Rice dehusking rolls, Oil extraction industry artifacts etc
Physical & mechanical properties
- Durometer or Hardness Range: 50 – 90 Shore A
- Tensile Strength Range: 1,000 – 3,500 PSI
- Elongation (Range %):250% – 600%
- Abrasion Resistance: Excellent
- Adhesion to Metal: Good to Excellent
- Adhesion to Rigid Materials: Good to Excellent
- Compression Set:Fair to Good
- Flex Cracking Resistance: Fair
- Impact Resistance: Good to Excellent
- Resilience / Rebound: Fair to Good
- Tear Resistance: Excellent
- Vibration Dampening:Fair to Good
Chemical resistance
- Acids, Dilute: Good
- Acids, Concentrated: Fair to Good
- Acids, Organic (Dilute): Good
- Acids, Organic (Concentrated): Poor
- Acids, Inorganic:Fair to Good
- Alcohol’s:Fair to Good
- Aldehydes:Poor to Fair
- Alkalies, Dilute: Good
- Alkalies, Concentrated: Poor to Good
- Amines: Poor
- Animal & Vegetable Oils: Good to Excellent
- Brake Fluids, Non-Petroleum Based:Poor
- Diester Oils:Fair to Good
- Esters, Alkyl Phosphate: Poor
- Esters, Aryl Phosphate: Poor to Fair
- Ethers: Poor
- Fuel, Aliphatic Hydrocarbon: Good to Excellent
- Fuel, Aromatic Hydrocarbon:Fair to Good
- Fuel, Extended (Oxygenated): Fair to Good
- Halogenated Solvents: Poor
- Hydrocarbon, Halogenated: Poor
- Ketones:Poor
- Lacquer Solvents:Fair
- LP Gases & Fuel Oils:Good to Excellent
- Mineral Oils:Good to Excellent
- Oil Resistance:Good to Excellent
- Petroleum Aromatic: Good
- Petroleum Non-Aromatic: Excellent
- Refrigerant Ammonia:Good
- Refrigerant Halofluorocarbons:R-11, R-12, R-13
- Refrigerant Halofluorocarbons w/ Oil: R-11, R-12
- Silicone:Oil Good
- Solvent Resistance: Good
Thermal properties
• Low Temperature Range: Up to -30 °C
• Minimum for Continuous Use (Static): -20 °C
• Brittle Point: —35 °C
• High Temperature Range: 90 °C to 105 °C
• Maximum for Continuous Use (Static):100 °C
Environmental performance
- Colorability: Good
- Flame Resistance: Poor
- Gas Permeability:Fair to Excellent
- Odor:Good
- Ozone Resistance:Fair
- Oxidation Resistance: Good
- Radiation Resistance: Fair to Good
- Steam Resistance: Fair to Good
- Sunlight Resistance: Poor to Good
- Taste Retention: Fair to Good
- Weather Resistance: Fair to Good
- Water Resistance: Good
Silicone Rubber (VMQ)
Silicone Rubber have excellent low temperature flexibility combined with outstanding high temperature resistance. Their service temperatures range from −70 °C to 250 °C.
Widely used in electrical-insulating properties, chemical stability, and the wide temperature range over which they retain resiliency, silicone rubbers are used mainly in O-rings, heat-resistant seals, caulks, gaskets, electrical insulators, flexible molds, and (owing to their chemical inertness) surgical implants.
Physical & mechanical properties
- Durometer or Hardness Range: 20 – 90 Shore A
- Tensile Strength Range: 200 – 1,500 PSI
- Elongation (Range %):100% – 900%
- Abrasion Resistance: Poor to Good
- Adhesion to Metal: Good
- Adhesion to Rigid Materials: Good
- Compression Set:Good to Excellent
- Flex Cracking Resistance: Poor to Good
- Impact Resistance: Poor to Good
- Resilience / Rebound: Good to Excellent
- Tear Resistance: Poor to Good
- Vibration Dampening:Fair to Good
Chemical resistance
- Acids, Dilute: Fair to Good
- Acids, Concentrated: Poor to Fair
- Acids, Organic (Dilute): Good
- Acids, Organic (Concentrated): Fair
- Acids, Inorganic:Fair to Good
- Alcohol’s:Fair to Good
- Aldehydes:Good
- Alkalies, Dilute: Poor to Good
- Alkalies, Concentrated: Poor to Excellent
- Amines: Good
- Animal & Vegetable Oils: Good to Excellent
- Brake Fluids, Non-Petroleum Based:Good
- Diester Oils:Poor to Fair
- Esters, Alkyl Phosphate: Good
- Esters, Aryl Phosphate: Good
- Ethers: Poor
- Fuel, Aliphatic Hydrocarbon: Poor to Fair
- Fuel, Aromatic Hydrocarbon:Poor
- Fuel, Extended (Oxygenated): Poor
- Halogenated Solvents: Poor
- Hydrocarbon, Halogenated: Poor
- Ketones:Poor
- Lacquer Solvents:Poor
- LP Gases & Fuel Oils:Fair
- Mineral Oils: Poor
- Oil Resistance: Fair
- Petroleum Aromatic: Fair
- Petroleum Non-Aromatic: Good
- Refrigerant Ammonia:Excellent
- Refrigerant Halofluorocarbons:Poor
- Refrigerant Halofluorocarbons w/ Oil: Poor
- Silicone Oil:Poor
- Solvent Resistance: Poor
Thermal properties
• Low Temperature Range: Upto -100 °C
• Minimum for Continuous Use (Static):-60 °C
• Brittle Point: -120 °C
• High Temperature Range: Up to 250 °C
• Maximum for Continuous Use (Static): 235 °C
Environmental performance
- Colorability: Excellent
- Flame Resistance: Fair to Excellent
- Gas Permeability:Poor to Fair
- Odor:Good
- Ozone Resistance:Excellent
- Oxidation Resistance: Excellent
- Radiation Resistance: Poor to Good
- Steam Resistance: Fair to Good
- Weather Resistance: Excellent
- Water Resistance: Excellent
Fluorosilicone Rubber (FVMQ)
VMQ has comparable physical properties to silicone rubber. Both compound types offer good weathering resistance, ozone resistance and extreme high- and low-temperature resistance. However, in terms of chemical resistance, fluorosilicone provides additional compatibility with aromatic mineral oils, fuels and low molecular weight aromatic hydrocarbons. In addition, some fluorosilicone types exhibit improved compression set.
Fluorosilicones provide a much wider operational temperature range from -70°F to 400°F (-57°C to 205°C). Many applications for fluorosilicones are in synthetic oils, gasoline and even extended fuels since its low temperature performance is much better than that of FKM’s.
Physical & mechanical properties
- Durometer or Hardness Range: 30 – 95 Shore A
- Tensile Strength Range: 500 – 3,000 PSI
- Elongation (Range %):450% – 600%
- Abrasion Resistance: Excellent
- Adhesion to Metal: Excellent
- Adhesion to Rigid Materials: Excellent
- Compression Set:Good to Excellent
- Flex Cracking Resistance: Good
- Impact Resistance: Excellent
- Resilience / Rebound: Good
- Tear Resistance: Fair to Excellent
- Vibration Dampening:Fair to Good
Chemical resistance
- Acids, Dilute: Excellent
- Acids, Concentrated: Good
- Acids, Organic (Dilute): Good
- Acids, Organic (Concentrated): Fair
- Acids, Inorganic:Fair
- Alcohol’s:Fair to Excellent
- Aldehydes:Poor
- Alkalies, Dilute: Excellent
- Alkalies, Concentrated: Good
- Amines: Poor
- Animal & Vegetable Oils: Excellent
- Brake Fluids, Non-Petroleum Based:Poor
- Diester Oils:Good to Excellent
- Esters, Alkyl Phosphate: Poor to Fair
- Esters, Aryl Phosphate: Good to Excellent
- Ethers Fair
- Fuel, Aliphatic Hydrocarbon: Excellent
- Fuel, Aromatic Hydrocarbon:Good to Excellent
- Fuel, Extended (Oxygenated): Excellent
- Halogenated Solvents: Good to Excellent
- Hydrocarbon, Halogenated: Good to Very Good
- Ketones:Poor
- Lacquer Solvents:Poor
- LP Gases & Fuel Oils:Excellent
- Mineral Oils:Good to Excellent
- Oil Resistance: Good
- Petroleum Aromatic: Good
- Petroleum Non-Aromatic: Good
- Refrigerant Ammonia:Excellent
- Refrigerant Halofluorocarbons:R-11, R-12
- Refrigerant Halofluorocarbons w/ Oil: R-11, R-12
- Silicone Oil:Excellent
- Solvent Resistance: Excellent
Thermal properties
• Low Temperature Range: Upto -60 °C
• Minimum for Continuous Use (Static): -50 °C
• Brittle Point: -80 °C
• High Temperature Range:Upto 210 °C
• Maximum for Continuous Use (Static):200 °C
Environmental performance
- Colorability:Good to Excellent
- Flame Resistance: Excellent
- Gas Permeability:Poor to Good
- Odor:Good
- Ozone Resistance:Excellent
- Oxidation Resistance: Excellent
- Radiation Resistance: Fair to Excellent
- Steam Resistance: Fair
- Sunlight Resistance: Excellent
- Taste Retention: Good
- Weather Resistance: Excellent
- Water Resistance: Excellent
Perfluoro elastomer (FFKM)
FFKM, contains higher amounts of fluorine than standard FKM, and features higher temperature ratings, up to approximately 325°C. FFKM also has improved chemical resistance, with nearly universal chemical compatibility.
This combination of high-performance capabilities makes FFKM seals the premium choice for the most challenging applications.
FFKM is used in o-rings and seals in environments with high temperatures and/or harsh chemicals in the aerospace, semiconductor, energy, pharmaceutical and industrial industries.
FFKMs receive greater elasticity due to their fluorinated backbone (and higher fluorine content than fluoroelastomer or FKM compounds), which makes them an excellent choice in a variety of demanding applications
Mechanical properties of FFKM
FFKM has excellent mechanical properties, but widely used because it has exceptional media and thermal performance. FFKM compounds are offered with a Shore A hardness of 60 to 90.
As FFKM is used mainly for O-rings or seals, its compression set is important.
The compression set of a typical FFKM compound with a Shore A hardness of about 70 is between 15 percent and 40 percent.
Tensile strength is generally between 10 and 20 MPa.
Elongation at break can be estimated at between 125 and 250 percent.
Thermal properties of FFKM
One of the great strengths of FFKM is its excellent heat performance. FFKM finished parts can be subjected to a temperature of up to +325 °C.
FFKM have very good shape-retaining recovery and compression set even at high temperatures. High temperatures can corrode rubber components and irreversibly damage the cross-linking structure. But produces stable results even at extremely high temperatures. The standard FFKM temperature range is therefore -8 °C to +325 °C.
FFKM is known as a material resistant to nearly all chemicals. This includes amines, esters, ketones and fuming HNO3, even resistant to fire-resistant hydraulic fluids. Exposed to oil, FFKM is stable at even extreme temperatures
FFKM is not resistant to alkali metals and per fluorinated hydrogen.
Nitrile Rubber (NBR)
Nitrile rubber (NBR), also called nitrile-butadiene rubber, an oil-resistant synthetic rubber produced from copolymer of acrylonitrile and butadiene. Its main applications are in fuel hoses, gaskets, rollers, and other products in which oil resistance is required.
Nitrile rubber is mostly used where high oil resistance is required, as in automotive seals, gaskets, or other items subject to contact with hot oils.
Physical & mechanical properties
- Durometer or Hardness Range: 20 – 95 Shore A
- Tensile Strength Range: 200 – 3,500 PSI
- Elongation (Range %):350% – 650%
- Abrasion Resistance: Good to Excellent
- Adhesion to Metal: Excellent
- Adhesion to Rigid Materials: Good to Excellent
- Compression Set:Good to Excellent
- Flex Cracking Resistance: Fair to Good
- Impact Resistance: Fair to Good
- Resilience / Rebound: Good
- Tear Resistance: Good to Excellent
- Vibration Dampening:Fair to Good
Chemical resistance
- Acids, Dilute: Good
- Acids, Concentrated: Poor to Fair
- Acids, Organic (Dilute): Good
- Acids, Organic (Concentrated): Poor
- Acids, Inorganic:Fair to Good
- Alcohol’s:Fair to Good
- Aldehydes:Poor to Fair
- Alkalies, Dilute: Good
- Alkalies, Concentrated: Poor to Good
- Amines: Poor
- Animal & Vegetable Oils: Good to Excellent
- Brake Fluids, Non-Petroleum Based:Poor
- Diester Oils:Fair to Good
- Esters, Alkyl Phosphate: Poor
- Esters, Aryl Phosphate: Poor to Fair
- Ethers: Poor
- Fuel, Aliphatic Hydrocarbon: Good to Excellent
- Fuel, Aromatic Hydrocarbon:Fair to Good
- Fuel, Extended (Oxygenated): Fair to Good
- Halogenated Solvents: Poor
- Hydrocarbon, Halogenated: Poor to Fair
- Ketones:Poor
- Lacquer Solvents:Fair
- LP Gases & Fuel Oils:Excellent
- Mineral Oils: Excellent
- Oil Resistance:Good to Excellent
- Petroleum Aromatic: Good
- Petroleum Non-Aromatic: Excellent
- Refrigerant Ammonia:Good
- Refrigerant Halofluorocarbons:R-11, R-12, R-13
- Refrigerant Halofluorocarbons w/ Oil: R-11, R-12
- Silicone Oil:Good
- Solvent Resistance: Good to Excellent
Thermal properties
- Low Temperature Range: Up to -40º C
- Minimum for Continuous Use (Static): -40 º C
- Brittle Point: -45 º C
- High Temperature Range: 100º C to 120º C
- Maximum for Continuous Use (Static): 110ºC
Environmental performance
- Colorability: Excellent
- Flame Resistance: Poor
- Gas Permeability:Fair to Excellent
- Odor:Good
- Ozone Resistance:Fair to Good
- Oxidation Resistance: Good
- Radiation Resistance: Fair to Good
- Steam Resistance: Fair to Good
- Sunlight Resistance: Poor to Good
- Taste Retention: Fair to Good
- Weather Resistance: Fair to Good
- Water Resistance: Good to Excellent
Styrene-butadiene rubber (SBR)
Styrene-butadiene rubber (SBR), a general-purpose synthetic rubber, produced from a copolymer of styrene and butadiene. SBR is used in great quantities in automobile and truck tires, generally as an abrasion-resistant replacement for natural rubber. It has excellent abrasion resistance, crack resistance, and better aging characteristics
Applications include belting, flooring, wire and cable insulation, and footwear etc
Physical & mechanical properties
- Durometer or Hardness Range: 30 – 95 Shore A
- Tensile Strength Range: 500 – 3,000 PSI
- Elongation (Range %):450% – 600%
- Abrasion Resistance: Excellent
- Adhesion to Metal: Excellent
- Adhesion to Rigid Materials: Excellent
- Compression Set:Good to Excellent
- Flex Cracking Resistance: Good
- Impact Resistance: Excellent
- Resilience / Rebound: Good
- Tear Resistance: Fair to Excellent
- Vibration Dampening:Fair to Good
Chemical resistance
- Acids, Dilute: Fair to Good
- Acids, Concentrated: Poor to Fair
- Acids, Organic (Dilute): Good
- Acids, Organic (Concentrated): Poor to Good
- Acids, Inorganic:Fair to Good
- Alcohol’s: Good
- Aldehydes:Poor to Fair
- Alkalies, Dilute: Fair to Good
- Alkalies, Concentrated: Fair to Good
- Amines:Poor to Good
- Animal & Vegetable Oils: Poor to Good
- Brake Fluids, Non-Petroleum Based:Poor to Good
- Diester Oils:Poor
- Esters, Alkyl Phosphate: Poor
- Esters, Aryl Phosphate: Poor
- Ethers: Poor
- Fuel, Aliphatic Hydrocarbon: Poor
- Fuel, Aromatic Hydrocarbon:Poor
- Fuel, Extended (Oxygenated): Poor
- Halogenated Solvents: Poor
- Hydrocarbon, Halogenated: Poor
- Ketones:Poor to Good
- Lacquer Solvents:Poor
- LP Gases & Fuel Oils:Poor
- Mineral Oils: Poor
- Oil Resistance: Poor
- Petroleum Aromatic: Poor
- Petroleum Non-Aromatic: Poor
- Refrigerant Ammonia:Good
- Refrigerant Halofluorocarbons:R-12, R-13
- Refrigerant Halofluorocarbons w/ Oil: Poor
- Silicone Oil:Poor
- Solvent Resistance: Poor
Thermal properties
• Low Temperature Range: Up to -50°C
• Minimum for Continuous Use (Static): – 45 °C
• Brittle Point: -55 °C
• High Temperature Range: 100 °C to 110 °C
• Maximum for Continuous Use (Static): 100°C
Environmental performance
- Colorability: Good
- Flame Resistance: Poor
- Gas Permeability:Fair
- Odor:Good
- Ozone Resistance:Poor
- Oxidation Resistance: Fair to Excellent
- Radiation Resistance: Poor to Good
- Steam Resistance: Fair to Good
- Sunlight Resistance: Poor
- Taste Retention: Fair to Good
- Weather Resistance: Fair to Good
- Water Resistance: Good to Excellent
Ethylene Propylene Rubber (EPDM)
Ethylene-propylene copolymer, also called ethylene-propylene rubber, a class of synthetic rubber produced by copolymerizing ethylene and propylene, usually in combination with other chemical compounds. EPDM has excellent resistance to electricity and ozone and an ability to be processed with a number of additives. They are made into products for use in automotive engines, electrical wiring, and construction
Widely employed in flexible seals for automobiles, wire and cable insulation, weather stripping, tire sidewalls, hoses, and roofing film.
Physical & mechanical properties
- Durometer or Hardness Range: 30 – 90 Shore A
- Tensile Strength Range: 500 – 2,500 PSI
- Elongation (Range %):100% – 700%
- Abrasion Resistance: Good
- Adhesion to Metal: Good to Excellent
- Adhesion to Rigid Materials: Good to Excellent
- Compression Set:Poor to Excellent
- Flex Cracking Resistance: Good
- Impact Resistance: Very Good
- Resilience / Rebound: Fair to Good
- Tear Resistance: Fair to Good
- Vibration Dampening:Fair to Good
Chemical resistance
- Acids, Dilute: Excellent
- Acids, Concentrated: Excellent
- Acids, Organic (Dilute): Excellen
- Acids, Organic (Concentrated): Fair to Good
- Acids, Inorganic:Excellent
- Alcohol’s:Good to Excellent
- Aldehydes:Good to Excellent
- Alkalies, Dilute: Excellent
- Alkalies, Concentrated: Excellent
- Amines:Fair to Good
- Animal & Vegetable Oils Good
- Brake Fluids, Non-Petroleum Based:Good to Excellent
- Diester Oils:Poor
- Esters, Alkyl Phosphate: Excellent
- Esters, Aryl Phosphate: Excellent
- Ethers: Fair
- Fuel, Aliphatic Hydrocarbon: Poor
- Fuel, Aromatic Hydrocarbon:Poor
- Fuel, Extended (Oxygenated): Poor
- Halogenated Solvents: Poor
- Hydrocarbon, Halogenated: Poor
- Ketones:Good to Excellent
- Lacquer Solvents:Poor
- LP Gases & Fuel Oils:Poor
- Mineral Oils: Poor
- Oil Resistance: Poor
- Petroleum Aromatic: Poor
- Petroleum Non-Aromatic: Poor
- Refrigerant Ammonia:Good
- Refrigerant Halofluorocarbons:R-12, R-13
- Refrigerant Halofluorocarbons w/ Oil: Poor
- Silicone Oil:Excellent
- Solvent Resistance: Poor
Thermal properties
• Low Temperature Range: Up to -50°C
• Minimum for Continuous Use (Static): -40°C
• Brittle Point: -55°C
• High Temperature Range: 100 °C to 120 °C
• Maximum for Continuous Use (Static): 100 °C
Environmental performance
- Colorability:Good to Excellent
- Flame Resistance: Poor
- Gas Permeability:Fair to Good
- Odor:Good
- Ozone Resistance:Good to Excellent
- Oxidation Resistance: Excellent
- Radiation Resistance: Good to Excellent
- Steam Resistance: Excellent
- Sunlight Resistance: Excellent
- Taste Retention: Good to Excellent
- Weather Resistance: Excellent
- Water Resistance: Excellent
Chloroprene Rubber (CR)
Neoprene (CR), also called polychloroprene or chloroprene rubber, synthetic rubber produced by the polymerization (or linking together of single molecules into giant, multiple-unit molecules) of chloroprene. A good general-purpose rubber, neoprene is valued for its high tensile strength, resilience, oil and flame resistance, and resistance to degradation by oxygen and ozone;
Principal applications are in products such as wire and cable insulation, hoses, belts, springs, flexible mounts, gaskets, and adhesives, where resistance to oil, heat, flame, and abrasion are required.
Physical & mechanical properties
- Durometer or Hardness Range: 20 – 95 Shore A
- Tensile Strength Range: 500 – 3,000 PSI
- Elongation (Range %):100% – 800%
- Abrasion Resistance:Very Good to Excellent
- Adhesion to Metal: Excellent
- Adhesion to Rigid Materials: Good to Excellent
- Compression Set:Poor to Good
- Flex Cracking Resistance: Good
- Impact Resistance: Good to Excellent
- Resilience / Rebound: Fair to Good
- Tear Resistance: Good to Excellent
- Vibration Dampening:Good to Excellent
Chemical resistance
- Acids, Dilute: Excellent
- Acids, Concentrated: Poor
- Acids, Organic (Dilute): Good to Excellent
- Acids, Organic (Concentrated): Poor to Good
- Acids, Inorganic:Good to Excellent
- Alcohol’s: Excellent
- Aldehydes:Poor to Fair
- Alkalies, Dilute: Good
- Alkalies, Concentrated: Poor
- Amines:Poor to Good
- Animal & Vegetable Oils: Good
- Brake Fluids, Non-Petroleum Based:Fair
- Diester Oils:Poor
- Esters, Alkyl Phosphate: Poor
- Esters, Aryl Phosphate: Poor to Fair
- Ethers: Poor
- Fuel, Aliphatic Hydrocarbon: Poor to Good
- Fuel, Aromatic Hydrocarbon:Poor to Fair
- Fuel, Extended (Oxygenated): Fair
- Halogenated Solvents: Poor
- Hydrocarbon, Halogenated: Poor
- Ketones:Poor to Fair
- Lacquer Solvents:Poor
- LP Gases & Fuel Oils:Good
- Mineral Oils: Fair to Good
- Oil Resistance: Fair
- Petroleum Aromatic: Good
- Petroleum Non-Aromatic: Good
- Refrigerant Ammonia:Excellent
- Refrigerant Halofluorocarbons:R-11, R-12, R-13, R-21, R-22
- Refrigerant Halofluorocarbons w/ Oil: R-11, R-12, R-22
- Silicone Oil:Fair to Excellent
- Solvent Resistance: Fair
Thermal properties
• Low Temperature Range: Up to -45°C
• Minimum for Continuous Use (Static): -35 °C
• Brittle Point: -60°C
• High Temperature Range: 100°C to 110 °C
• Maximum for Continuous Use (Static): 110 °C
Environmental performance
- Colorability: Fair
- Flame Resistance: Fair to Good
- Gas Permeability:Fair to Good
- Odor:Fair to Good
- Ozone Resistance:Good to Excellent
- Oxidation Resistance: Good to Excellent
- Radiation Resistance: Fair to Good
- Steam Resistance: Fair to Good
- Sunlight Resistance: Good to Excellent
- Taste Retention: Fair to Good
- Weather Resistance: Fair to Good
- Water Resistance: Fair to Good
Epichlorohydrin Rubber (ECO)
Epichlorohydrin rubber (ECO) is the modern alternative for PVC/NBR with greater heat resistance of up to 130°C at constant operating temperature with the added advantages of improved ozone and acid resistance.
ECO has properties similar to nitrile rubber but with better heat, oil and petrol resistance. It has low gas permeability and better low temperature flexibility than NBR. It has excellent resistance to acids, alkalis and ozone.
However, it suffers from poor compression set and has a corrosive effect on metals which can increase tooling costs and limit metal bonding applications.
Physical & mechanical properties
- Durometer or Hardness Range: 40 – 90 Shore A
- Tensile Strength Range: 500 – 2,500 PSI
- Elongation (Range %):200% – 800%
- Abrasion Resistance: Fair to Good
- Adhesion to Metal: Fair to Good
- Adhesion to Rigid Materials: Fair to Excellent
- Compression Set:Good to Excellent
- Flex Cracking Resistance: Good
- Impact Resistance: Fair to Excellent
- Resilience / Rebound: Good
- Tear Resistance: Fair to Excellent
- Vibration Dampening:Good
Chemical resistance
- Acids, Dilute: Good
- Acids, Concentrated: Poor to Fair
- Acids, Organic (Dilute): Fair
- Acids, Organic (Concentrated): Poor
- Acids, Inorganic:Fair to Good
- Alcohol’s:Fair to Good
- Aldehydes:Poor
- Alkalies, Dilute: Poor
- Alkalies, Concentrated: Fair to Good
- Amines:Poor to Good
- Animal & Vegetable Oils: Excellent
- Brake Fluids, Non-Petroleum Based:Poor
- Diester Oils:Poor to Good
- Esters, Alkyl Phosphate: Poor
- Esters, Aryl Phosphate: Poor
- Ethers: Good
- Fuel, Aliphatic Hydrocarbon: Good to Excellent
- Fuel, Aromatic Hydrocarbon:Good to Excellent
- Fuel, Extended (Oxygenated): Fair to Good
- Halogenated Solvents: Poor
- Hydrocarbon, Halogenated: Excellent
- Ketones:Fair
- Lacquer Solvents:Fair
- LP Gases & Fuel Oils:Excellent
- Mineral Oils: Excellent
- Oil Resistance: Excellent
- Petroleum Aromatic: Good to Excellent
- Petroleum Non-Aromatic: Poor
- Refrigerant Ammonia:Poor
- Refrigerant Halofluorocarbons:R-12
- Refrigerant Halofluorocarbons w/ Oil: Good to Excellent
- Silicone Oil:Good to Excellent
- Solvent Resistance: Good to Excellent
Thermal properties
• Low Temperature Range: Up tp -35 °C
• Minimum for Continuous Use (Static): -25°C
• Brittle Point: -45 °C
• High Temperature Range: 100 °C to 125 °C
• Maximum for Continuous Use (Static): 120 °C
Environmental performance
- Colorability: Good
- Flame Resistance: Poor to Good
- Gas Permeability:Excellent
- Odor:Good
- Ozone Resistance:Good to Excellent
- Oxidation Resistance: Good to Excellent
- Radiation Resistance: Poor
- Steam Resistance: Fair to Good
- Sunlight Resistance: Good
- Taste Retention: Good
- Weather Resistance: Good
- Water Resistance: Good
Fluorcarbon Rubber (FKM)
FKM (also known as FPM in Europe) rubber compounds are frequently used to resist extreme temperatures and harsh chemicals. The strong carbon-fluorine bonds that make up the polymer structure provide high thermo-chemical resistance, giving excellent ageing characteristics, such aslow compression set at elevated temperatures.
FKM offers excellent resistance to mineral oils and greases, aliphatic, aromatic and some chlorinated hydrocarbons, fuels, silicone oils and greases. Fluorocarbon rubber compounds are available as a copolymer, terpolymer & tetrapolymes
FKM materials for use in low temperature applications, where with a glass transition of -40°C, it is possible to use FKM down to -51°C in service.
Specific grades are also available for use in biofuels,
Types of FKM
FKM Type | Classification Name | Cure system | Fluorine content | Description |
---|---|---|---|---|
Type 1 | FKM A | Bisphenol | 66% | General Purpose with Excellent Mechanical Properties |
Type 2 | FKM B, F, GF | Bisphenol & Peroxide | 60-70% | Improved Oil/ fluid, solvent resistance, Fuel resistance. Peroxide cure provides improved coolant and water resistance |
Type 3 | GLT | Peroxide | 64-67% | Improved low temperature but less chemical resistance |
Type 4 | Aflas | Peroxide | 55% | Excellent resistance to lubricating oils, corrosion inhibitors and coolants |
Physical & mechanical properties
- Durometer or Hardness Range: 50 – 95 Shore A
- Tensile Strength Range: 500 – 2,000 PSI
- Elongation (Range %):400% – 500%
- Abrasion Resistance: Fair to Good
- Adhesion to Metal: Good to Excellent
- Adhesion to Rigid Materials: Fair to Good
- Compression Set:Good to Excellent
- Flex Cracking Resistance: Fair to Good
- Impact Resistance: Good
- Resilience / Rebound: Poor to Fair
- Tear Resistance: Fair to Good
- Vibration Dampening:Fair to Good
Environmental performance
- Colorability:Good to Excellent
- Flame Resistance: Good to Excellent
- Gas Permeability:Good to Excellent
- Odor:Good
- Ozone Resistance:Excellent
- Oxidation Resistance: Excellent
- Radiation Resistance: Fair to Good
- Steam Resistance: Good to Excellent
- Sunlight Resistance: Good to Excellent
- Taste Retention: Fair to Good
- Weather Resistance: Excellent
- Water Resistance: Excellent
Chemical resistance depends on the type of FKM grade.
Acrylic Rubber (ACM)
Polyacrylic elastomers, also called ACM rubbers, are synthetic elastomers composed of acrylic monomers. ACM has outstanding resistance to heat, oxidation and hydraulic oils, good resistance to ozone, and weathering which is superior to nitrile rubber.
However, water and moisture resistance is poor, as is resistance to acids and alkalis. Also low temperature applications are usually limited to approximately -10°C due to low cold temperature flexibility and compression set.
ACM elastomers are primarily used where combined resistance to heat and oils is required. They are often a good alternative to more expensive heat resistant elastomers where service is less than 150 °C.
Typical applications include automotive transmission components like seals and hoses that have to be resistant to hot oil, fuel and many other common automotive lubricants and hydraulic fluids. ACM elastomer have also found use in vibration damping due to its excellent resilience. Other applications include textiles, adhesives, and coatings.
Physical & mechanical properties
- Durometer or Hardness Range: 40-90 Shore A
- Tensile Strength Range: 500 – 2,500 PSI
- Elongation (Range%): 100% – 450%
- Abrasion Resistance: Fair to Good
- Adhesion to Metal: Fair to Good
- Flex Cracking Resistance: Fair to Good
- Impact Resistance: Poor
- Resilience/Rebound: Fair to Good
- Tear Resistance: Poor to Good
- Vibration Dampening: Good to Excellent
Thermal properties
• Low Temperature Range: Up tp -30 °C
• Minimum for Continuous Use (Static): -25°C
• Brittle Point: -45 °C
• High Temperature Range: 150 °C to 175 °C
• Maximum for Continuous Use (Static): 150 °C
Chemical resistance
- Acids, Dilute: Fair
- Acids, Concentrated: Poor to Fair
- Acids, Organic (Concentrated): Poor
- Alcohols: Poor Adhesion to Rigid Materials: Fair to Good
- Aldehydes: Poor Compression Set: Poor to Good
- Alkalies, Dilute: Fair
- Alkalies, Concentrated: Fair
- Amines: Poor
- Animal & Vegetable Oils: Good
- Brake Fluids, Non-Petroleum Based: Poor
- Diester Oils: Good
- Esters, Alkyl Phosphate: Poor
- Esters, Aryl Phosphate: Poor
- Esthers: Poor
- Fuel, Aliphatic Hydrocarbon: Excellent
- Fuel, Aromatic Hydrocarbon: Poor to Good
- Ketones (MEK, acetone): Poor to Good
- Lacquer Solvents: Poor to Good
- LP Gases & Fuel Oils: Good
- Mineral Oils: Good to Excellent
- Oil Resistance: Excellent
- Petroleum Aromatic: Fair
- Petroleum Non-Aromatic: Good
- Refrigerant Ammonia: Fair
- Refrigerant Halofluorocarbons: R-11, R-12, R-13
- Refrigerant Halofluorocarbons w/ Oil: R-11, R-12 , R-13, R22
- Silicone Oil: Excellent
- Water Resistance: Excellent
- Solvent Resistance: Good
Environmental performance
- Colorability: Good
- Flame Resistance: Poor
- Odor: Fair to Good
- Gas Permeability: Good to Excellent
- Ozone Resistance: Good to Excellent
- Oxidation Resistance: Good to Excellent
- Radiation Resistance: Poor to Good
- Steam Resistance Poor
- Sunlight Resistance: Good to Excellent
- Weather Resistance: Excellent
Ethylene-Acrylic Rubber (AEM VAMAC)
Ethylene-acrylic monomer is a terpolymer of ethylene, methyl acrylate, and an acid-containing monomer as a cure site. AEM can replace silicone in certain applications especially high volume requirements where economies of scale are required.
AEM offers high heat resistance, excellent ozone and weather resistance, low temperature flexibility and high tensile strength.
Typical applications are air management, vacuum and engine breather and oil hoses.
AEM, as excellent vibration dampening, excellent heat aging characteristics and good dynamic property retention over a wide, temperature range, resistant to oils, transmission fluids, water, glycol mixtures, and alkalis.
Physical & mechanical properties
- Durometer or Hardness Range: 35 – 95 Shore A
- Tensile Strength Range: 500 – 3,000 PSI
- Elongation (Range %):200% – 850%
- Abrasion Resistance: Good to Excellent
- Adhesion to Metal: Good
- Adhesion to Rigid Materials: Good
- Compression Set:Poor to Good
- Flex Cracking Resistance: Good
- Impact Resistance: Good to Very Good
- Resilience / Rebound: Poor to Fair
- Tear Resistance: Good to Excellent
- Vibration Dampening:Good
Chemical resistance
- Acids, Dilute: Good
- Acids, Concentrated: Poor to Fair
- Acids, Organic (Dilute): Good to Excellent
- Acids, Organic (Concentrated): Poor to Excellent
- Acids, Inorganic:Fair to Good
- Alcohol’s:Good to Excellent
- Aldehydes:Fair to Good
- Alkalies, Dilute: Good to Excellent
- Alkalies, Concentrated: Poor
- Amines: Good
- Animal & Vegetable Oils: Good
- Brake Fluids, Non-Petroleum Based:Poor
- Diester Oils:Poor
- Esters, Alkyl Phosphate: Poor
- Esters, Aryl Phosphate: Poor
- Ethers: Poor
- Fuel, Aliphatic Hydrocarbon: Good
- Fuel, Aromatic Hydrocarbon:Poor to Fair
- Fuel, Extended (Oxygenated): Fair
- Halogenated Solvents: Poor to Good
- Hydrocarbon, Halogenated: Poor
- Ketones:Poor
- Lacquer Solvents:Poor
- LP Gases & Fuel Oils:Poor
- Mineral Oils: Poor
- Oil Resistance: Poor
- Petroleum Aromatic: Poor
- Petroleum Non-Aromatic: Poor
- Refrigerant Ammonia:Poor to Good
- Refrigerant Halofluorocarbons:Poor to Good
- Refrigerant Halofluorocarbons w/ Oil: Poor
- Silicone Oil:Good to Excellent
- Solvent Resistance: Poor
Thermal properties
• Low Temperature Range: Up to -40 °C
• Minimum for Continuous Use (Static): -30 °C
• Brittle Point: -45 °C
• High Temperature Range: 150 °C to 175 °C
• Maximum for Continuous Use (Static): 150 °C
Environmental performance
- Colorability: Good
- Flame Resistance: Poor
- Gas Permeability:Excellent
- Odor:Good
- Ozone Resistance:Excellent
- Oxidation Resistance: Excellent
- Radiation Resistance: Good
- Steam Resistance: Poor to Fair
- Sunlight Resistance: Excellent
- Taste Retention: Fair to Good
- Weather Resistance: Excellent
- Water Resistance: Good to Excellent
Hydrogenated Nitrile Rubber (HNBR)
HNBR is made via selective hydrogenation of the NBR butadiene groups which improves the temperature and ozone resistance considerably. HNBR is widely known for its physical strength and retention of properties after long-term exposure to heat, oil, and chemicals. HNBR has better heat resistance; oxidation resistance; tensile strength and abrasion resistance than standard nitrile (NBR). Also an excellent choice for automotive refrigerant service.
HNBR is resistant to hot water and steam and has good high- and low-temperature performance with regard to its physical properties. In addition, these mixes also have high media and abrasion resistance and good mechanical properties.
Physical & mechanical properties
- Durometer or Hardness Range: 30 – 95 Shore A
- Tensile Strength Range: 1,500 – 3,500 PSI
- Elongation (Range %):90% – 550%
- Abrasion Resistance: Good to Excellent
- Adhesion to Metal: Excellent
- Adhesion to Rigid Materials: Good to Excellent
- Compression Set:Good to Excellent
- Flex Cracking Resistance: Fair to Good
- Impact Resistance: Excellent
- Resilience / Rebound: Good
- Tear Resistance: Good to Excellent
- Vibration Dampening:Fair to Good
Chemical resistance
- Acids, Dilute: Good
- Acids, Concentrated: Fair to Good
- Acids, Organic (Dilute): Good
- Acids, Organic (Concentrated): Fair to Good
- Acids, Inorganic:Fair to Good
- Alcohol’s:Good to Excellent
- Aldehydes:Fair to Good
- Alkalies, Dilute: Good
- Alkalies, Concentrated: Poor to Good
- Amines: Good
- Animal & Vegetable Oils: Good to Excellent
- Brake Fluids, Non-Petroleum Based:Fair
- Diester Oils:Good
- Esters, Alkyl Phosphate: Poor
- Esters, Aryl Phosphate: Poor to Fair
- Ethers:Poor to Fair
- Fuel, Aliphatic Hydrocarbon: Excellent
- Fuel, Aromatic Hydrocarbon:Fair to Good
- Fuel, Extended (Oxygenated): Good to Excellent
- Halogenated Solvents: Poor to Fair
- Hydrocarbon, Halogenated: Poor
- Ketones:Poor
- Lacquer Solvents:Fair
- LP Gases & Fuel Oils:Excellent
- Mineral Oils:Good to Excellent
- Oil Resistance:Good to Excellent
- Petroleum Aromatic: Good to Excellent
- Petroleum Non-Aromatic: Good to Excellent
- Refrigerant Ammonia:Good
- Refrigerant Halofluorocarbons:R-11, R-12, R-13
- Refrigerant Halofluorocarbons w/ Oil: R-11, R-12
- Silicone Oil:Good to Excellent
- Solvent Resistance: Poor
Thermal properties
• Low Temperature Range: Up to -40 °C
• Minimum for Continuous Use (Static): -30 °C
• Brittle Point: -50 °C
• High Temperature Range: 130 °C to 150 °C
• Maximum for Continuous Use (Static): 135 °C
Environmental performance
- Colorability: Excellent
- Flame Resistance: Poor
- Gas Permeability:Fair to Excellent
- Odor:Good
- Ozone Resistance:Good to Excellent
- Oxidation Resistance: Excellent
- Radiation Resistance: Fair to Good
- Steam Resistance: Fair to Good
- Sunlight Resistance: Good to Excellent
- Taste Retention: Fair to Good
- Weather Resistance: Good to Excellent
- Water Resistance: Excellent
Carboxylated Nitrile (XNBR)
XNBR is a nitrile rubber (NBR) with the addition of a carboxyl group to saturate the butadiene segment of the carbon polymer backbone. The added carboxyl group greatly improves the resistance of NBR to abrasive and tear wear without affecting its oil and solvent resistance or its thermal stability.
XNBR based parts are usually applied in dynamic assembly such as seals and rod wipers, V- belts, High abrasion resistance shoes, O-rings, Printing rolls, Rice dehusking rolls, Oil extraction industry artifacts etc
Physical & mechanical properties
- Durometer or Hardness Range: 50 – 90 Shore A
- Tensile Strength Range: 1,000 – 3,500 PSI
- Elongation (Range %):250% – 600%
- Abrasion Resistance: Excellent
- Adhesion to Metal: Good to Excellent
- Adhesion to Rigid Materials: Good to Excellent
- Compression Set:Fair to Good
- Flex Cracking Resistance: Fair
- Impact Resistance: Good to Excellent
- Resilience / Rebound: Fair to Good
- Tear Resistance: Excellent
- Vibration Dampening:Fair to Good
Chemical resistance
- Acids, Dilute: Good
- Acids, Concentrated: Fair to Good
- Acids, Organic (Dilute): Good
- Acids, Organic (Concentrated): Poor
- Acids, Inorganic:Fair to Good
- Alcohol’s:Fair to Good
- Aldehydes:Poor to Fair
- Alkalies, Dilute: Good
- Alkalies, Concentrated: Poor to Good
- Amines: Poor
- Animal & Vegetable Oils: Good to Excellent
- Brake Fluids, Non-Petroleum Based:Poor
- Diester Oils:Fair to Good
- Esters, Alkyl Phosphate: Poor
- Esters, Aryl Phosphate: Poor to Fair
- Ethers: Poor
- Fuel, Aliphatic Hydrocarbon: Good to Excellent
- Fuel, Aromatic Hydrocarbon:Fair to Good
- Fuel, Extended (Oxygenated): Fair to Good
- Halogenated Solvents: Poor
- Hydrocarbon, Halogenated: Poor
- Ketones:Poor
- Lacquer Solvents:Fair
- LP Gases & Fuel Oils:Good to Excellent
- Mineral Oils:Good to Excellent
- Oil Resistance:Good to Excellent
- Petroleum Aromatic: Good
- Petroleum Non-Aromatic: Excellent
- Refrigerant Ammonia:Good
- Refrigerant Halofluorocarbons:R-11, R-12, R-13
- Refrigerant Halofluorocarbons w/ Oil: R-11, R-12
- Silicone:Oil Good
- Solvent Resistance: Good
Thermal properties
• Low Temperature Range: Up to -30 °C
• Minimum for Continuous Use (Static): -20 °C
• Brittle Point: —35 °C
• High Temperature Range: 90 °C to 105 °C
• Maximum for Continuous Use (Static):100 °C
Environmental performance
- Colorability: Good
- Flame Resistance: Poor
- Gas Permeability:Fair to Excellent
- Odor:Good
- Ozone Resistance:Fair
- Oxidation Resistance: Good
- Radiation Resistance: Fair to Good
- Steam Resistance: Fair to Good
- Sunlight Resistance: Poor to Good
- Taste Retention: Fair to Good
- Weather Resistance: Fair to Good
- Water Resistance: Good
Silicone Rubber (VMQ)
Silicone Rubber have excellent low temperature flexibility combined with outstanding high temperature resistance. Their service temperatures range from −70 °C to 250 °C.
Widely used in electrical-insulating properties, chemical stability, and the wide temperature range over which they retain resiliency, silicone rubbers are used mainly in O-rings, heat-resistant seals, caulks, gaskets, electrical insulators, flexible molds, and (owing to their chemical inertness) surgical implants.
Physical & mechanical properties
- Durometer or Hardness Range: 20 – 90 Shore A
- Tensile Strength Range: 200 – 1,500 PSI
- Elongation (Range %):100% – 900%
- Abrasion Resistance: Poor to Good
- Adhesion to Metal: Good
- Adhesion to Rigid Materials: Good
- Compression Set:Good to Excellent
- Flex Cracking Resistance: Poor to Good
- Impact Resistance: Poor to Good
- Resilience / Rebound: Good to Excellent
- Tear Resistance: Poor to Good
- Vibration Dampening:Fair to Good
Chemical resistance
- Acids, Dilute: Fair to Good
- Acids, Concentrated: Poor to Fair
- Acids, Organic (Dilute): Good
- Acids, Organic (Concentrated): Fair
- Acids, Inorganic:Fair to Good
- Alcohol’s:Fair to Good
- Aldehydes:Good
- Alkalies, Dilute: Poor to Good
- Alkalies, Concentrated: Poor to Excellent
- Amines: Good
- Animal & Vegetable Oils: Good to Excellent
- Brake Fluids, Non-Petroleum Based:Good
- Diester Oils:Poor to Fair
- Esters, Alkyl Phosphate: Good
- Esters, Aryl Phosphate: Good
- Ethers: Poor
- Fuel, Aliphatic Hydrocarbon: Poor to Fair
- Fuel, Aromatic Hydrocarbon:Poor
- Fuel, Extended (Oxygenated): Poor
- Halogenated Solvents: Poor
- Hydrocarbon, Halogenated: Poor
- Ketones:Poor
- Lacquer Solvents:Poor
- LP Gases & Fuel Oils:Fair
- Mineral Oils: Poor
- Oil Resistance: Fair
- Petroleum Aromatic: Fair
- Petroleum Non-Aromatic: Good
- Refrigerant Ammonia:Excellent
- Refrigerant Halofluorocarbons:Poor
- Refrigerant Halofluorocarbons w/ Oil: Poor
- Silicone Oil:Poor
- Solvent Resistance: Poor
Thermal properties
• Low Temperature Range: Upto -100 °C
• Minimum for Continuous Use (Static):-60 °C
• Brittle Point: -120 °C
• High Temperature Range: Up to 250 °C
• Maximum for Continuous Use (Static): 235 °C
Environmental performance
- Colorability: Excellent
- Flame Resistance: Fair to Excellent
- Gas Permeability:Poor to Fair
- Odor:Good
- Ozone Resistance:Excellent
- Oxidation Resistance: Excellent
- Radiation Resistance: Poor to Good
- Steam Resistance: Fair to Good
- Weather Resistance: Excellent
- Water Resistance: Excellent
Fluorosilicone Rubber (FVMQ)
VMQ has comparable physical properties to silicone rubber. Both compound types offer good weathering resistance, ozone resistance and extreme high- and low-temperature resistance. However, in terms of chemical resistance, fluorosilicone provides additional compatibility with aromatic mineral oils, fuels and low molecular weight aromatic hydrocarbons. In addition, some fluorosilicone types exhibit improved compression set.
Fluorosilicones provide a much wider operational temperature range from -70°F to 400°F (-57°C to 205°C). Many applications for fluorosilicones are in synthetic oils, gasoline and even extended fuels since its low temperature performance is much better than that of FKM’s.
Physical & mechanical properties
- Durometer or Hardness Range: 30 – 95 Shore A
- Tensile Strength Range: 500 – 3,000 PSI
- Elongation (Range %):450% – 600%
- Abrasion Resistance: Excellent
- Adhesion to Metal: Excellent
- Adhesion to Rigid Materials: Excellent
- Compression Set:Good to Excellent
- Flex Cracking Resistance: Good
- Impact Resistance: Excellent
- Resilience / Rebound: Good
- Tear Resistance: Fair to Excellent
- Vibration Dampening:Fair to Good
Chemical resistance
- Acids, Dilute: Excellent
- Acids, Concentrated: Good
- Acids, Organic (Dilute): Good
- Acids, Organic (Concentrated): Fair
- Acids, Inorganic:Fair
- Alcohol’s:Fair to Excellent
- Aldehydes:Poor
- Alkalies, Dilute: Excellent
- Alkalies, Concentrated: Good
- Amines: Poor
- Animal & Vegetable Oils: Excellent
- Brake Fluids, Non-Petroleum Based:Poor
- Diester Oils:Good to Excellent
- Esters, Alkyl Phosphate: Poor to Fair
- Esters, Aryl Phosphate: Good to Excellent
- Ethers Fair
- Fuel, Aliphatic Hydrocarbon: Excellent
- Fuel, Aromatic Hydrocarbon:Good to Excellent
- Fuel, Extended (Oxygenated): Excellent
- Halogenated Solvents: Good to Excellent
- Hydrocarbon, Halogenated: Good to Very Good
- Ketones:Poor
- Lacquer Solvents:Poor
- LP Gases & Fuel Oils:Excellent
- Mineral Oils:Good to Excellent
- Oil Resistance: Good
- Petroleum Aromatic: Good
- Petroleum Non-Aromatic: Good
- Refrigerant Ammonia:Excellent
- Refrigerant Halofluorocarbons:R-11, R-12
- Refrigerant Halofluorocarbons w/ Oil: R-11, R-12
- Silicone Oil:Excellent
- Solvent Resistance: Excellent
Thermal properties
• Low Temperature Range: Upto -60 °C
• Minimum for Continuous Use (Static): -50 °C
• Brittle Point: -80 °C
• High Temperature Range:Upto 210 °C
• Maximum for Continuous Use (Static):200 °C
Environmental performance
- Colorability:Good to Excellent
- Flame Resistance: Excellent
- Gas Permeability:Poor to Good
- Odor:Good
- Ozone Resistance:Excellent
- Oxidation Resistance: Excellent
- Radiation Resistance: Fair to Excellent
- Steam Resistance: Fair
- Sunlight Resistance: Excellent
- Taste Retention: Good
- Weather Resistance: Excellent
- Water Resistance: Excellent
Perfluoro elastomer (FFKM)
FFKM, contains higher amounts of fluorine than standard FKM, and features higher temperature ratings, up to approximately 325°C. FFKM also has improved chemical resistance, with nearly universal chemical compatibility.
This combination of high-performance capabilities makes FFKM seals the premium choice for the most challenging applications.
FFKM is used in o-rings and seals in environments with high temperatures and/or harsh chemicals in the aerospace, semiconductor, energy, pharmaceutical and industrial industries.
FFKMs receive greater elasticity due to their fluorinated backbone (and higher fluorine content than fluoroelastomer or FKM compounds), which makes them an excellent choice in a variety of demanding applications
Mechanical properties of FFKM
FFKM has excellent mechanical properties, but widely used because it has exceptional media and thermal performance. FFKM compounds are offered with a Shore A hardness of 60 to 90.
As FFKM is used mainly for O-rings or seals, its compression set is important.
The compression set of a typical FFKM compound with a Shore A hardness of about 70 is between 15 percent and 40 percent.
Tensile strength is generally between 10 and 20 MPa.
Elongation at break can be estimated at between 125 and 250 percent.
Thermal properties of FFKM
One of the great strengths of FFKM is its excellent heat performance. FFKM finished parts can be subjected to a temperature of up to +325 °C.
FFKM have very good shape-retaining recovery and compression set even at high temperatures. High temperatures can corrode rubber components and irreversibly damage the cross-linking structure. But produces stable results even at extremely high temperatures. The standard FFKM temperature range is therefore -8 °C to +325 °C.
FFKM is known as a material resistant to nearly all chemicals. This includes amines, esters, ketones and fuming HNO3, even resistant to fire-resistant hydraulic fluids. Exposed to oil, FFKM is stable at even extreme temperatures
FFKM is not resistant to alkali metals and per fluorinated hydrogen.
Research & development
Our team has been engaged in manufacturing, formulation design, research and development of new materials for many years. Also, we cooperate with DuPont, The Dow Chemical Company, The Chemours Company, Solvay Specialty Polymers in Europe, ZEON in Japan, etc. which from world-famous chemical manufacturers to become the rubber compounding plant recognised in the Asia-Pacific region.
Our principles have set up a professional rubber laboratory that is conformed to the TAF accreditation of the National Accreditation Foundation, based on the different demand of customers in various countries and the American material specifications (ASTM, MIL, UL, AMS), German material specifications (DIN), Japanese material specifications (JIS ). We provide professional research development and technical services that conform the demand of international standards.
Research & development
Microtype Fourier Transform Infrared Spectroscopy (IN10)
Fourier Transform Infrared Spectroscopy (AVATAR 330)
Thermogravimetric analysis (Q500)
Thermogravimetric analysis (i1000)
Differential scanning calorimetry (Q20)
Thermomechanical Analysis
Scanning Electron Microscope-Energy Dispersive Spectrometer (6000 Plus)
Pyrolysis-Gas Chromatography-Mass Spectrometry
X-ray Fluorescence Spectrometer
Our Certifications
Proudly accredited, our certifications attest to our commitment to quality, precision, and environmental responsibility, reinforcing our promise of excellence in every rubber solution we deliver.
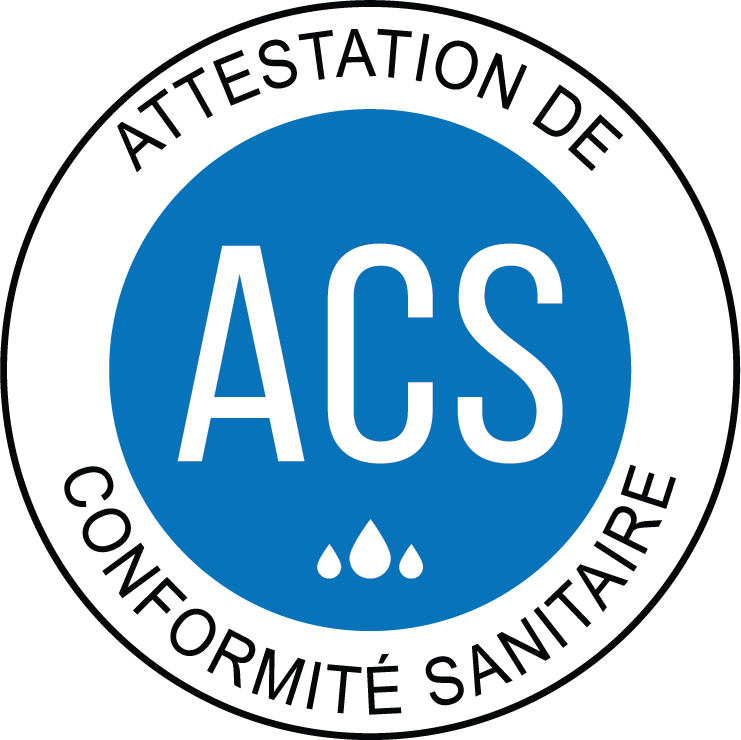
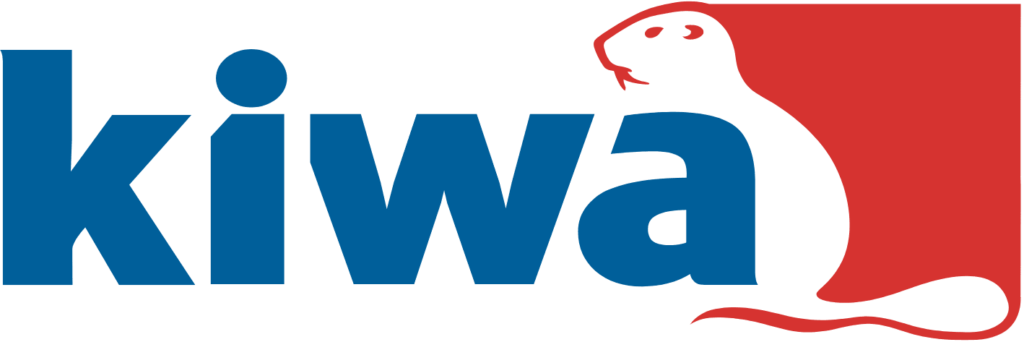
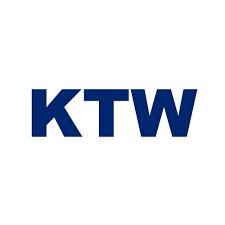
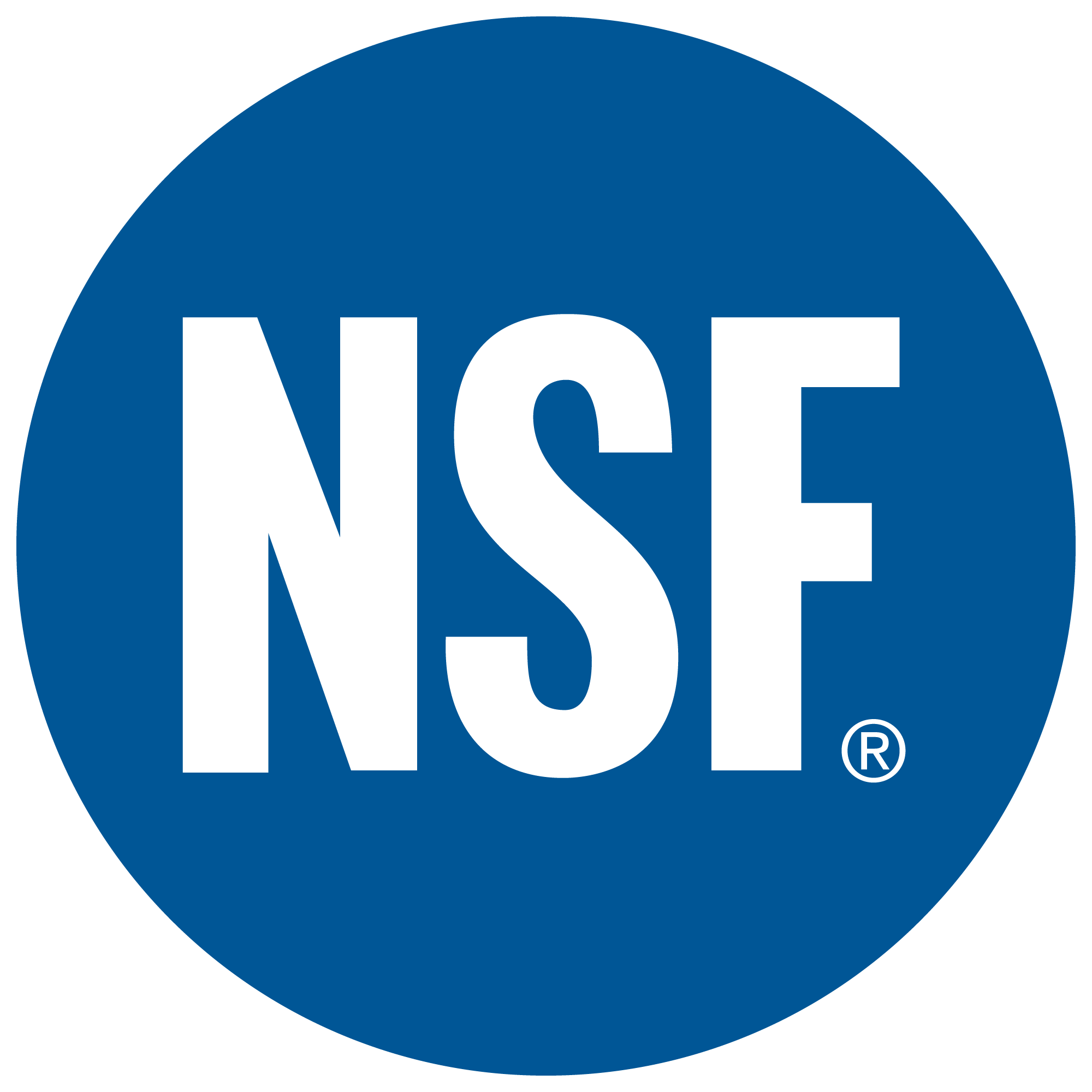
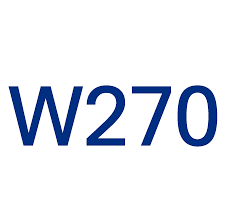
Drinking Water Certifications
Product number | Material | Cure system | Hardness | Certification |
---|---|---|---|---|
EP02971PWRC | EPDM | Peroxide | 70 | ACS |
EP02971PWRC | EPDM | Peroxide | 70 | KTW |
EP02971PWRC | EPDM | Peroxide | 70 | KTW-W270 |
EP02971PWRC | EPDM | Peroxide | 70 | NSF |
EP02971PWRC | EPDM | Peroxide | 70 | WRAS |
EP01961PWRC | EPDM | Peroxide | 60 | WRAS |
EP01961PWRC | EPDM | Peroxide | 60 | ACS |
EP01961PWRC | EPDM | Peroxide | 60 | NSF |
NB03973PWRC | NBR | Peroxide | 70 | WRAS |
NB03973PWRC | NBR | Peroxide | 70 | NSF |
NB03973PWRC | NBR | Peroxide | 70 | KTW-W270 |
NB03973PWRC | NBR | Peroxide | 70 | KTW |
EP05280PWRC | EPDM | Peroxide | 80 | WRAS |
NB07973WRC | NBR | Sulfur | 70 | NSF |
EP01873WRC | EPDM | Sulfur | 70 | NSF |
NB07471T(EN549) | NBR | Sulfur | 70 | EN549 B1H3 |
NB04171Q | NBR | Sulfur | 70 | EN549 B2H3 |
NB09869WRC | NBR | Sulfur | 70 | WRAS |